- Inexpensive plastic prototypes
- Parts designed using specialty materials
- Parts with intricate geometrical requirements
- When a quick turnaround is needed
Table of Contents
6 Steps to Get Your Project Started.
The Fundamentals of CNC Machining:
What Is CNC Machining?
How is CNC Machining Different From Other Machining Methods?
3-Axis v. 5-Axis Machining Basics
Designing for CNC Machining
CNC Machining Materials Basics
Fundamentals of CNC Machining
CNC machining methods are capable of producing parts with a high level of accuracy and with superior physical properties.
From metals to plastics to wood, this versatile technology is appropriate for just about any material.
And because so much of the CNC machining process is automated, it offers highly competitive pricing for projects that involve one-off, custom parts or for mid-range-volume productions.
To get from concept to manufacturing, it’s helpful to have a solid foundation of knowledge about what CNC machining is and its many applications.
Take an in-depth look at how design, method, and materials affect turnaround times and costs, and how to choose the right ones for your project.
What Is CNC Machining?
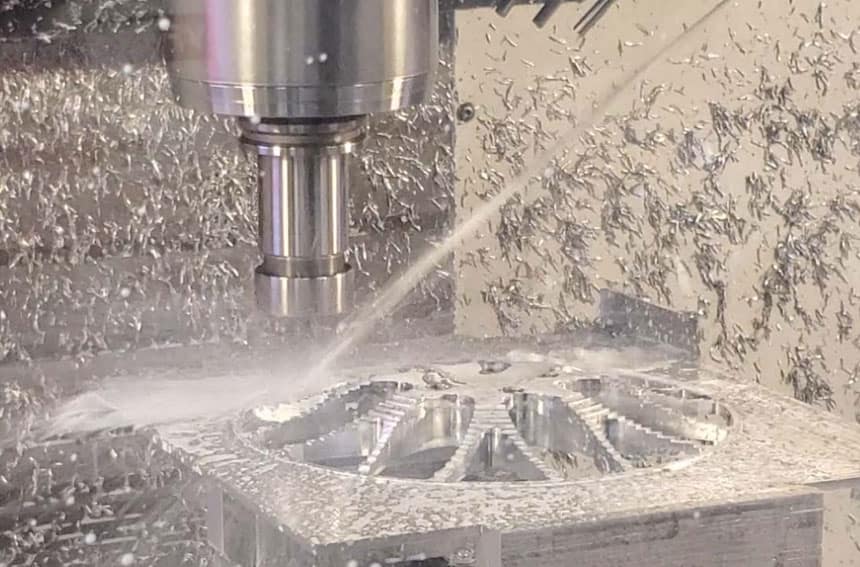
CNC Machining is a digital technology that uses CAD (Computer Aided Design) files to manufacture parts. Unlike additive or formative technologies like 3D and injection molding, it uses material removal methods to form the final product.
CNC machining has a number of applications including:
- Space
- Aerospace
- Automotive
- Product Design & Development
- Electrical & Electronic Manufacturing
- Tooling & Industrial Manufacturing
- Sports & Motorsports
Basic Process:
- An engineer designs a CNC-compatible CAD model.
- The CAD model is converted into a CNC program by a machinist.
- An automated CNC system performs all the machining, removing material to execute the final design.
How is CNC Machining Different From Other Machining Methods?
Sometimes it’s easier to understand this machining approach in the context of other, similar methods to better understand what CNC machining is and whether it’s right for your project.
3D Printing
Is Good For:
Other Considerations:
3D printing isn’t typically appropriate for large volume projects since the unit price is stable and so volume discounts don’t apply.
Forming Technology
Is Good For:
- Projects that seek economy of scale
- Extremely high-volume metal part projects
- Extremely high-volume plastic parts
Other Considerations:
Forming technology methods are typically cost-effective for 1,000 or more parts.
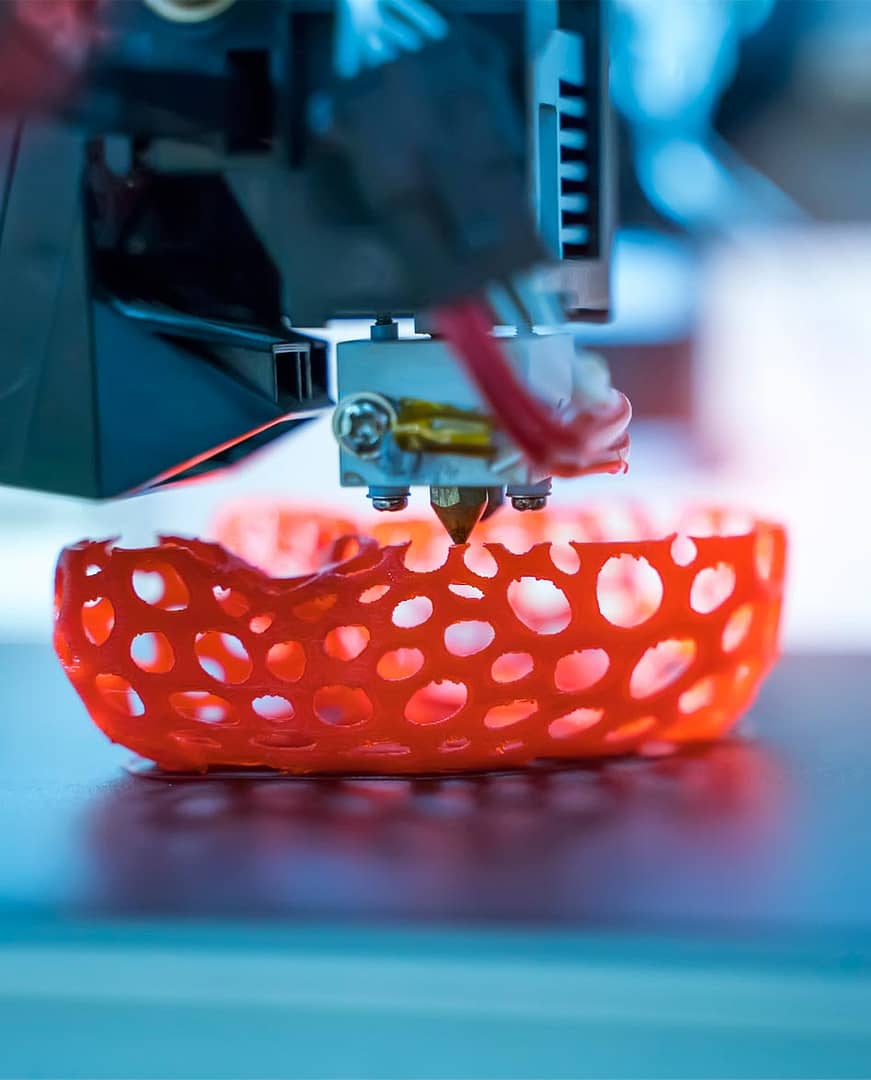
CNC Machining
Is Good For:
- Designs conducive to metal
- Designs with relatively simple geometry
- Small-to-medium volume projects
- One-off projects
- Designs that require a high level of dimensional accuracy
Other Considerations:
Because CNC start-up costs are fixed and can be spread over multiple parts, designers can take advantage of economies of scale. However, costs go up with more complex geometries.
3-Axis v. 5-Axis Machining Basics
3-Axis and 5-Axis machining are broad terms that encompass a range of methods for removing materials using cutting tools, and each are ideal for different types of projects.
3-Axis Machining
There are two basic system variations for 3-Axis machining:
- CNC Milling
- CNC Turning (Lathes)
There are a number of distinguishing factors between the two, and they each have benefits and limitations depending on the type of project being machined.
As a rule, most parts with simple geometries can be produced with 3-axis CNC milling technology and can be manufactured with a high level of accuracy and with extremely tight tolerances.
Typically, CNC 3-axis turning can accommodate very high volume production requirements at the lowest cost per unit than any other CNC machining method.
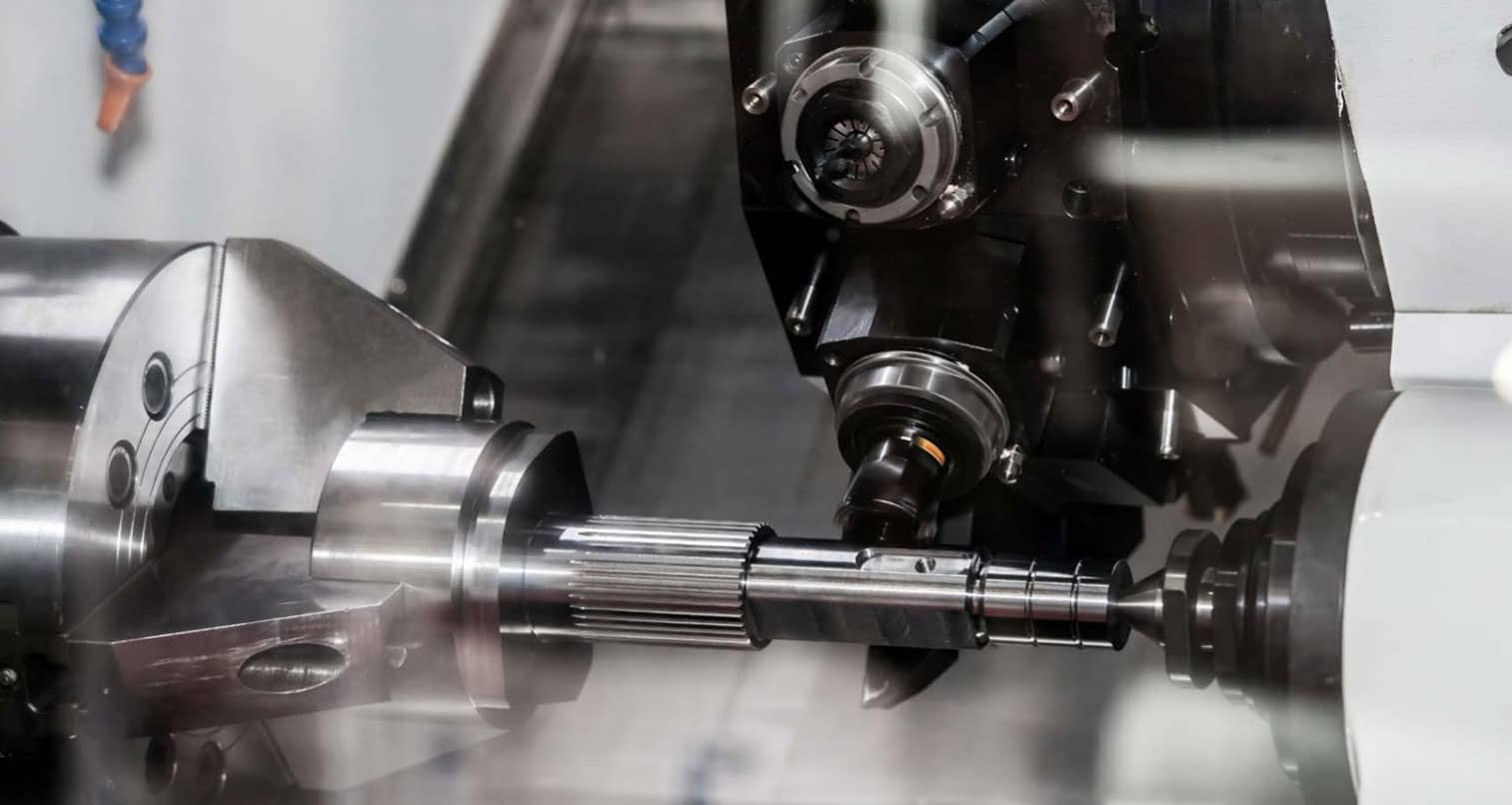
5-Axis Machining
There are three system variations for multi-axis CNC machining, but they’re all fundamentally based on milling or lathing technology:
- 5-Axis indexed milling
- Continuous 5-axis milling
- Mill-turning centers with live tooling
5-axis milling or lathing machines offer a wider degree of freedom than 3-axis CNC machines, and with this technology, a part with multiple geometric profiles can be produced in one single step.
5-Axis milling technology comes with a slightly higher price tag, not just because of the advanced capabilities it offers and the necessary expertise required to execute those capabilities, but because specialized machinery is needed to produce parts.
Designing for CNC Machining
Although this machining method is highly versatile, it’s ideal to have a basic understanding of best practices for designing CNC machining projects since this technology is limited by some restrictions.
Basic Areas of Restriction:
- Tool access
- Tool geometry & stiffness
- Workholding
- Workpiece stiffness
Additionally, there are recommendations and feasibility aspects to consider when designing for CNC machining projects.
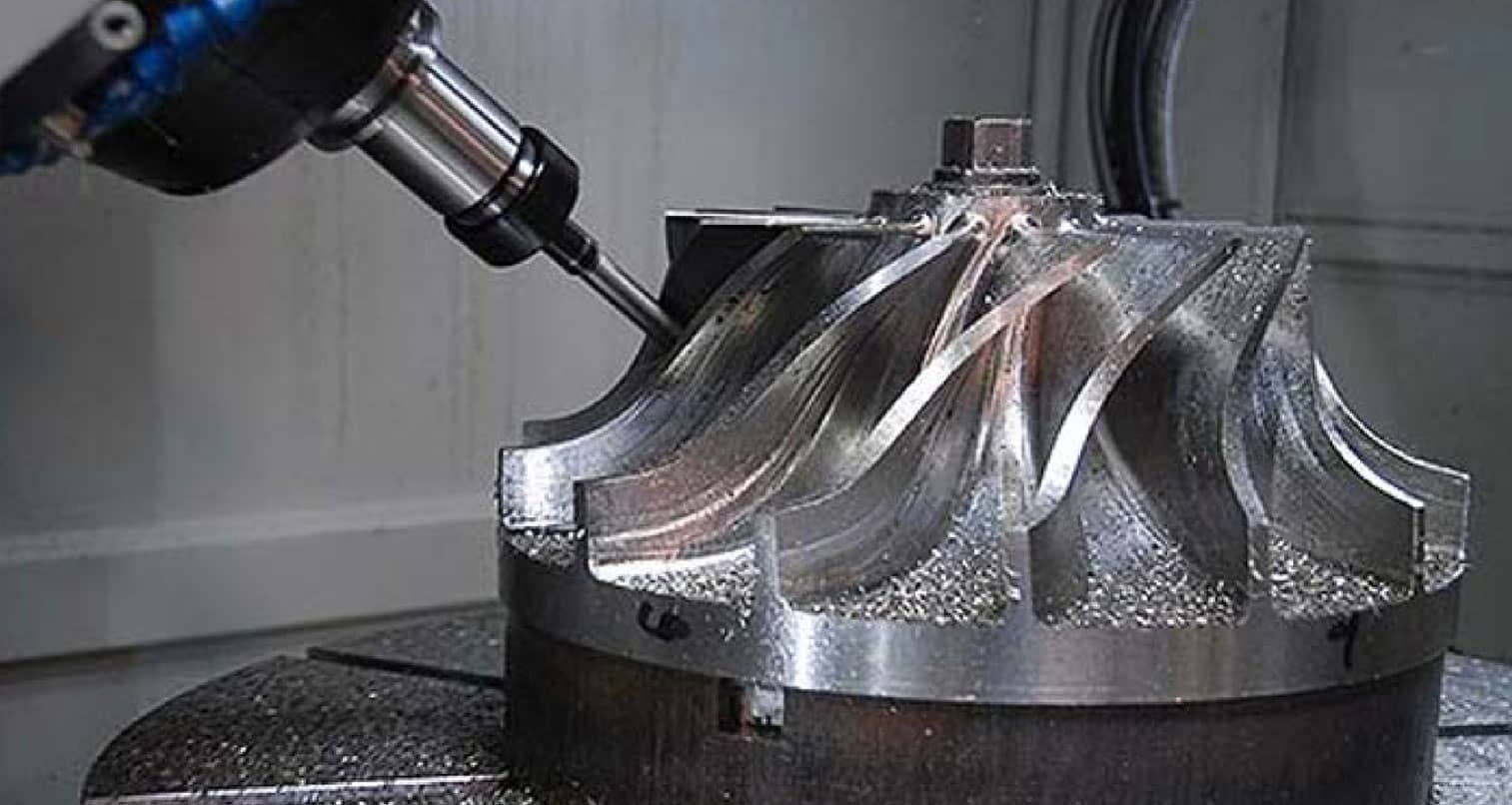
Some Basic Design Rules:
- Tall features are prone to vibrations which makes them difficult to machine accurately.
- Cavities and pockets should be designed with feasible depths in mind, especially in the case of deeper cavities.
- For internal vertical edges, the larger the fillet the better.
- Recommendations and feasibility limitations for wall thickness apply for both plastics and metals.
- Holes are limited by diameter and depth.
- Threads require a technical drawing in the order.
- Micro-machining elements should be avoided unless necessary.
- Unilateral, bilateral, interference or geometric tolerances should absolutely be defined on all critical features.
- Dimension plays a big role in designing for undercuts with the recommendation being that they’re designed with widths in whole millimeter increments (or standard inch fractions).
CNC Machining Materials Basics
Providing they are hard enough, almost any material can be CNC machined. But selecting the material is crucial in the design process depending on the specific use for the part as well as design requirements.
Basic Areas of Restriction:
- Tool access
- Tool geometry & stiffness
- Workholding
- Workpiece stiffness
Additionally, there are recommendations and feasibility aspects to consider when designing for CNC machining projects.
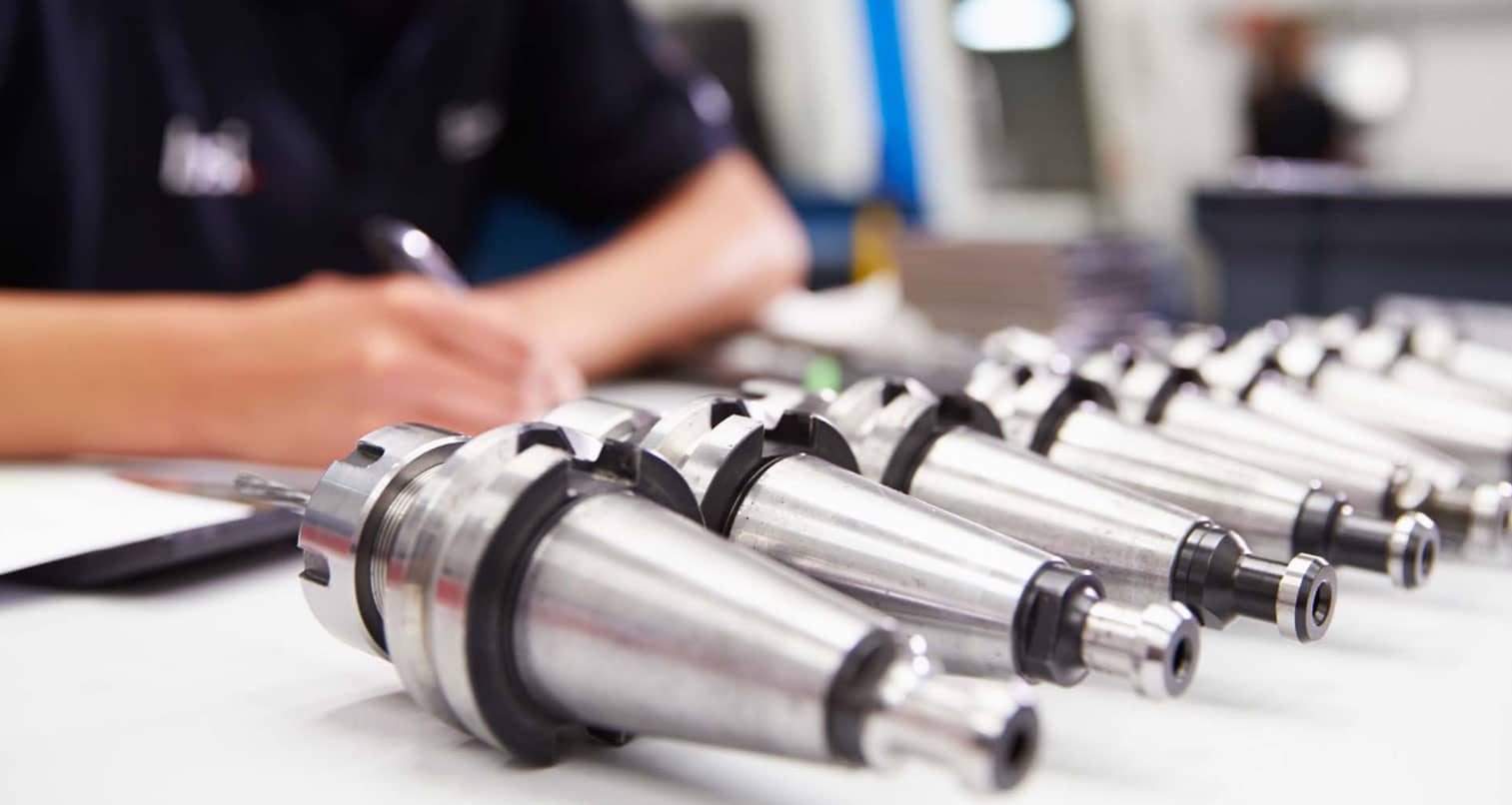
Some Basic Design Rules:
- Tall features are prone to vibrations which makes them difficult to machine accurately.
- Cavities and pockets should be designed with feasible depths in mind, especially in the case of deeper cavities.
- For internal vertical edges, the larger the fillet the better.
- Recommendations and feasibility limitations for wall thickness apply for both plastics and metals.
- Holes are limited by diameter and depth.
- Threads require a technical drawing in the order.
- Micro-machining elements should be avoided unless necessary.
- Unilateral, bilateral, interference or geometric tolerances should absolutely be defined on all critical features.
- Dimension plays a big role in designing for undercuts with the recommendation being that they’re designed with widths in whole millimeter increments (or standard inch fractions).